This instruction manual is intended to be a guide when operating the T600 Extreme Seam welder. To ensure optimal performance from your welder, please follow the recommendations and specifications precisely.
Table of Contents
- Chapter 1: Intended Use
- Chapter 2: Explanation of Warnings
- Chapter 3: Electrical and Air Requirements
- Chapter 4: Principles of Heat Sealing
- Chapter 5: Definition of Controls
- Chapter 6: Recommended Replacement Parts
- Chapter 7: Machine Specifications
- Chapter 8: Maintenance
- Chapter 9: Transportation Specs and Storage
- Chapter 10: Technical Requirements
- Chapter 11: Additional Machine Documents
For more technical information regarding this machine call our Resolution Center at 1-855-888-WELD or email service@weldmaster.com.
1.0 Intended Use
The T600 is a rotary hot air welding machine intended to heat-seal weldable thermal plastics such as:
- Vinyl (PVC) laminated and coated fabrics
- Vinyl (PVC) and Polyurethane (PU) films
- Polyurethane (PU) and Polypropylene (PP) coated fabric
- Polyethylene (PE)
- Thermoplastic rubber (TPR) film and fabrics
- Non-woven Polyester and Polypropylene
- Various Fusing Tapes
- Weldable Webbing
- Rigid Extruded Products
The manufacturer does not approve of:
- Any other uses for these machines.
- The removal of any safety guards while in operation.
- Unauthorized modification of the machines.
- Using replacement parts that are not manufacturer-approved.
Only a properly-trained technician may operate and/or perform any routine maintenance orrepairs to the machines.
NOTE: The manufacturer will not be held liable for any damage or injuries occurring from any inappropriate use of this machine.
2.0 Explanation of Warnings
There are several different warning symbols placed on the Miller Weldmaster T600. The symbols are to alert the operator of potentially hazardous areas on the machine. Familiarize yourself with their placement and meaning.
Caution: Hot
The “Caution: Hot” symbol is placed on a guard nearhot surfaces.
Danger: Pinch Points
The “Danger: Pinch Points” symbol is placed near any potential pinch points. Do not place any body parts near these sections of the machine while the machine is running.
Caution: Unplug Machine
The “Caution: Unplug Machine” sticker is placed near the opening of the cabinet and all access panels. To prevent electrocution, the machine should always have the power disconnected before the cabinet door is open.
Warning: Keep Hands Clear
The“Warning: Keep Hands Clear” sticker is placed on the Heater Assembly. To prevent any pinching or burns, be aware of the location of your hands at all times.
Warning: High Temperature Air
The “Warning: High Temperature Air” sticker is placed on the Heater Assembly.
Caution: Electricity
The “Caution: Electricity” sticker is placed near areas that contain electrical.
3.0 Electrical and Air Requirements
Warning! Only a qualified electrician may connect the electrical power.
Warning! Only a qualified electrician may connect the electrical power.
Preparation - World Power
-
Make sure the Power Supply is at 230v, 25amp, 50/60hz or 400v, 16amp, 50/60hz and the Pressure Supply comes up to 120 psi (8.3 bar) when the machine is working.
-
Make sure the voltage and current is dedicated to the machine and to the above specification.
-
An appropriate ground connection must be made to the ground terminal provided on the machine.
-
Before operation of the machine be sure the surrounding area of the machine is free of flammable debris. Only authorized persons should be in the area of the machine while in use.
-
In the event of an emergency, press the Emergency Stop Button.
Electrical Supply
Due to the number of different style outlets available, the cord will not include a plug. It is recommended that your electrician install a plug that is comparable to your style power outlet. You may choose to have your power cord hard-wired into your Power Supply. It is recommended that your electrician use a Junction Box with an ON/OFF switch. The Miller Weldmaster T300 requires one of the following electrical requirements:
- 25 Amp - Single phase - 230 Volts
- 16 Amp - Single phase - 400 Volts
Shop Air Supply
The Miller Weldmaster T300 includes an In-Shop Air Supply Valve that allows quick connects and disconnects to your shop air supply. Due to the number of different style airline connectors, a male quick-connect is not included. You will want to select a male quick-connect with a ¼ inch NPT (National Pipe Thread) to match your female quick-connect. The Miller Weldmaster T600 requires the following shop air requirements:
- Minimum of 5 cfm at 120 psi
- Not to exceed 140 liters/min at 8.3 Bar
- An in-line water and dirt separator
4.0 Principals of Heat Sealing
Heat
Hot Air Heating System
The Heat required for the welding operation is created electrically by one heating element located inside the Heat Element Housing. The Internal Air Compressor pumps air over the heat element and carries the heat through the Hot Air Nozzle, applying the heat to the material to be welded. The hot air temperature ranges from 25 to 730 Degrees Celsius (100 to 1350 Degrees Fahrenheit).
Hot Wedge Heating System
The Hot Wedge heat system uses four cartridge heat elements to electrically heat the Wedge. The Hot Wedge temperature ranges from 25 to 490 Degrees Celsius (100 to 915 Degrees Fahr- enheit).
Speed
The Speed of the Weld Rollers determines the amount of time the heat is applied to the material being welded. The slower the speed setting, the more the material will be heated. The faster the speed setting, the less the material will be heated. To achieve the best weld, a minimal amount of heat should be applied to the material while still achieving a full weld. Too much heat will cause distortion of the material; while not enough heat will prevent the material from welding.
Pressure
The pressure of the weld roller is the final step when creating a weld. The pressure of the weld roller compresses the heated material together completing the welding process.
Summary
When heat sealing, the correct combination of heat, speed, and pressure will allow you to achieve a properly welded seam.
5.0 Definition of Controls
Main Screen - HMI Operation
Recipe Number: This is a particular combination of the parameters of heat and speed used to weld different types of fabric. This shows which recipe you’re currently using on the machine. 0 - 25 Available recipe settings. In order to change recipes the heat on/off switch must be in the off position.
Machine Speed: This is the speed of the Weld Roller. The speed can be adjusted by pressing the up or down arrows. Each push of the button increases or decreases the speed by .01 m/min. If you hold the buttons for 1 second, it will increase or decrease the speed by .1 m/min.
Actual Temperature: This is how hot the machine is currently.
Temperature Set Point: This is how hot you want the machine to be for the purpose of welding your thermal plastics.
Heat Switch: This is for turning the Temperature Controller ON/OFF.
Heat Swing Button: Turns the Heat Swing ON/OFF. The swing-arm will not swing in when this is set to OFF.
Puller Switch: Turns the Out Board Puller ON/OFF. The puller will remain in the up position and will not turn when in the off position.
Menu Screen - Welding Functions
This screen is to adjust the speed percentages of the Upper Roller and Puller Roller. When all of the rollers are in sync, the speed shows 100.0%. Adjust the percentages to change the speeds of each individual roller. The actual speed of the roller can be checked at the Machine Speed Display Screen.
Auto-Reverse: This adjusts the reverse speed of the rollers when the machine stops welding. This function is to minimize missed welding and make a perfect product. The UP and DOWN arrows increase and decrease the reverse speed.
ON/OFF Switches: The Drive FWD/REV, Drive System ON/OFF, and Foot Pedal Override ON/OFF switches are used to turn the functions ON/OFF.
Delay Settings: These are used to eliminate voids in seam.
Drive Start Delay Time: Once the foot pedal is depressed, the Drive Start Delay Time will delay the weld rollers from turning until the set point is reached. The Drive Start Delay Time will be adjusted by the operator to the desired setting.
Drive Stop Delay Time: Once the foot pedal is released, the weld rollers will continue to turn until the Roller Stop Delay Time has reached the set point. The Roller Stop Delay Time will be adjusted by the operator to the desired setting.
Auto-Reverse Time: Once the foot pedal is released, the weld rollers will turn in reverse until the Roller Stop Delay Time has reached the set point and the Auto-Reverse time has reached the set point. The Auto-reverse Time will be adjusted by the operator to the desired setting.
Auto-Reverse: This adjusts the reverse speed of the rollers when the machine stops welding. This function is to minimize missed welding and make a perfect product. The UP and DOWN arrows increase and decrease the reverse speed.
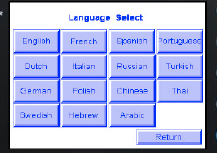
Password Change: The machine administrator may change the machine’s eight-digit password.
Temperature Parameter: For adjusting the PID (Proportional Integral Derivative) value.
- KP = Proportion Factor
- TI = Integral Time
- TD = Rate Time
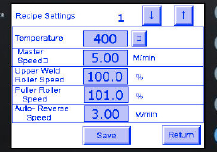
Hi-Temp Limit: Maximum heating temperature of the machine. Once the actual temperature is out of this limit, the machine will stop heating automatically.
Over-Temp Alarm: When the actual temperature is higher than the Over-Temp Alarm Temperature, there is an on-screen alarm that notifies the operator.
MAX Output: Limits the amount of output power to the heating system.
NOTE: There are two different PID parameters saved in the machine according to heating system used, hot air or hot wedge. Press the Default for 1 second, and the PID will go back to the factory settings.
Hour Meter: The hour meter will count total time of which the heating system is on.
Recipe Settings: When changing parameters, pressing the SAVE button will save the adjusted settings to the selected recipe.
6.0 Recommended Replacement Parts
Miller Weldmaster recommends keeping the following spare parts in stock:
NOTE: There are two different PID parameters saved in the machine according to heating system used, hot air or hot wedge. Press the Default for 1 second, and the PID will go back to the factory settings.
Parts Order? Call 855-888-9353 or email service@weldmaster.com
The T600 is a heat sealing machine which welds thermal plastic fabrics or films by Hot Air or Hot Wedge, through applying pressure, consistent speed, and accurate temperature for perfectly sealing thermal plastic materials.
Features
- Suitable for multiple-sized tents, inflatable boats, banners, tarps, awnings, and etc.
- User Friendly HMI allows the operators to easily adjust the machine for a wide variety of products.
- Auto-Control Temperature controller allows the system to accurately provide heat to the products being produced.
- Dual Pedal Control allows for easy operation for extended periods of time with high efficiency.
- An automatic Auto Reverse function allows the machine to start and stop with a void free seam.
Technical Specifications
- Amp Rating - 25amp at 230volt / 16amp at 400 volt
- Rated Power - 4000 W
- Rated Voltage - 230v AC, 50/60hz or 400v AC, 50/60hz
- Maximum Temperature - 1350°F (730°C)
- General Air Pressure - 120psi (8.3 bar)
- Machine Speed - 3 ft/min to 80 ft/min (1 m/min to 25 m/min)
- Overall Dimensions - 69in x 26in x 58in (1750mm x 650mm x 1450mm)
- Seal Width - 5mm to 50 mm
- Maximum Noise - 70 dbA
- Net Weight - 730lbs (330kg)
- Electrical Document Number - The documentation number is the serial number of the machine. This number is located on the serial tag on the machine.
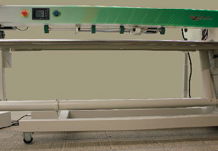
Mechanical Section
- Removable Roller Table Top: The roller table top assembly is used for paneling applications, edging, edge finishing, and general seaming applications.
- Swing Arm: The swing arm is used when products include shapes, curves, and tubes of the seaming area.
Heat Source
- Hot Air: heat element housing contains the heating element and thermal-couple.
- Hot Wedge: hot wedge tip contains the heating elements and thermal-couple.
- Upper Unit: Upper Weld Roller up and down motion.
- Heat System Adjustment Assembly: Allows for accurate positioning of the Hot Air Nozzle or wedge tip.
- Outboard Fabric Puller Assembly: Assists operator with material handling while producing flatter seams.
Operator Controls Section
- Control Panel: The HMI (Human Machine Interface) Digital Touch Screen allows you to set system controls.
- Power On/Off Button: Power button turns the machine on and off.
- Emergency Stop: The emergency stop button, when depressed, will stop the seaming operation in the event of an emergency.
Pneumatic System
- Pressure Adjustment Regulator: Filters out water and dirt in the air. The Pressure Adjusting regulator, regulates the pressure to the machine. Increase the pressure by rotating clock-wise, and decrease the value by rotating counter-clockwise.
- Solenoid Valve: Controls the actions of the Air Cylinders.
- Pressure Gauge: Used for displaying the pressure setting. The Upper Weld Roller gauge is used for displaying the pressure setting of the Upper Weld Roller.
- Air Cylinder: The upper unit/puller Air Cylinders are used for opening and closing the weld roller and puller roller. The heat system cylinder controls swing-in and swing-out of the heat system.
- Puller Pressure Limit Control: Reference page 21 for adjustment procedure.
Other
- Power Supply Circuit Breaker: Used for the protective control of the General Power Supply of the complete machine.
- Right Pedal Switch: It controls the lifting of the weld roller, and the opening and closing of the weld rollers and puller (if the puller switch is on).
- Left Pedal Switch: Controls the starting and stopping of the seaming operation.
8.0 Maintenance
Warning! The operator must disconnect the power from the machine before proceeding.
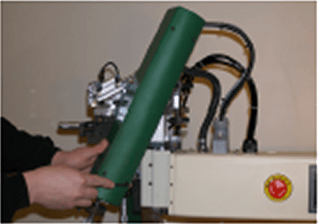
1. Loosen and remove the protective cover from the element housing.
2. Unpack the fiberglass insulation around the front of the element housing. Be cautious to avoid eye contact when handling the insulation.
3. Loosen and remove the two bolts to the bracket holding the element housing in place.
4. Remove the bolt securing the element in the housing.
6. Pull out the element vertically.
7. Replace the old element with a new element by following the procedure in reverse. When reinstalling the element, be sure to align the key to the slot of the element housing to the element.
NOTE: The glass tube is easily broken and can already be broken, be very careful.
Electrical Circuits
- When replacing parts and components, you must use the part or components of the same type as the original or equivalent to the original type. Original equip ment replacement parts should be purchased through Miller Weldmaster and or a Miller Weldmaster authorize distributor.
- The electrical cabinet must be cleaned every six months. To properly clean the electrical cabinet: disconnect the power supply, using compressed air and a blow gun, gently blow air across the electrical component and control cabinet cleaning dust and debris from the area.
- To avoid damaging the PLC, Display and Operating Panel, never plug or unplug the cables connecting the PLC, Display and Operating Panel while the power is on.
- If there is any fault that cannot be removed, please immediately contact the service department at Miller Weldmaster.
Drive System
- Check if the Driving Sprockets are dislocated or loosened.
- Check if the chains are too loose. Tighten as needed.
- Check if the nozzle is parallel with and at the center of the Weld Roller. If not, it shall be adjusted as per Hot Air Heat System Adjustment.
- Check if the up and down movement of the Upper Unit is smooth.
NOTICE: The glass tube is easily broken and can already be broken, be very careful.
Cleaning/Replacing Air Filter (For Hot Air Machines Only)
The Miller Weldmaster T600 has an external air compressor that supplies airflow to the heat element. Periodic cleaning and changing of the Air Filter Cartridge is necessary to maintain sufficient airflow. Insufficient airflow or any impurities in the airflow will shorten the life of the heat element.
Clean Air Filter Cartridge Every Week
If the surrounding conditions in your production area are not clean, it is recommended that you clean the Air Filter Cartridge twice a week.
- Loosen and remove the Air Filter Cartridge End Cap.
- Remove the Air Filter Cartridge.
- Using brake cleaner or a product containing high amounts of Ether, spray the Air Filter Cartridge from the inside out.
- Dry the Air Filter Cartridge by blowing the Air Filter Cartridge from the inside out with shop air.
- Reinstall the Air Filter Cartridge and Air Filter Cartridge End Cap onto the internal air compressor and tighten.
Replace Air Filter Cartridge Every 3 - 6 Months
If the surrounding conditions in your production area are not clean, it is recommended that you change the Air Filter Cartridge every month.
- Remove the Air Filter Cartridge End Cap.
- Remove the Air Filter Cartridge.
- Replace with a new Air Filter Cartridge, part number 330297.
- Reinstall the Air Filter Cartridge and Air Filter Cartridge End Cap onto the internal air compressor.
Tightening/Oiling Chains
The Miller Weldmaster T300 has several chains that are used to drive weld rollers and puller rollers. Although not a high maintenance item, chains should be inspected once a year to ensure there is not excessive corrosion, rust, or dirt. Also inspect for any looseness or slack. If needed, lubricate chains once a year with 80w – 90w gear oil.
1. Turn the circuit breaker to the off position.
2. Disconnect the power cord from the power supply. If the power cord is hard wired, shut the power supply off at the junction box.
3. Remove the cover on the end cabinet and inspect the chains. Perform any maintenance to the chains as needed.
4. Remove the end caps on the lower beam and inspect the chains. Perform any maintenance to the chains as needed.
5. Remove the out puller cover and weld roller upper unit covers. Perform any maintenance to the chains as needed.
Replacing Wedge Tip
1. Remove power to the machine by switching the main circuit breaker to the off position.
2. Ensure the wedge has cooled down to a temperature that can be handled.
3. Loosen and remove the housing cover.
4. Disconnect the male from the female leads on the thermocouple and wedge wires.
5. Loosen the two set screws located on the side of the wedge.
6. Remove both bolts from the rear mounting bracket and remove the wedge assembly.
7. Install the new wedge assembly reversing the above instructions. When tightening the bolts to the rear of the wedge, loosen by a 1/8 of a turn so the wedge has some “float” to it.
Hot Air Heat System Adjustments
Begin by turning your hot air on and setting to the desired temperature. Set weld rollers to the closed position by engaging the Weld Roller Pedal.
- Left to right nozzle position, check this by engaging the Drive Foot Pedal and watch the tip of the nozzle. It should be centered left to right on the weld rollers, if so, move on to next alignment step. If not, locate the left to right Lockdown Knob and loosen by two turns. This will allow adjustment of the left to right Micrometer. Now locate the left to right Micrometer which is located about eye level with the operator. Rotating the left to right Micrometer Knob so the numeric value is increasing will move the nozzle tip to the left. Rotating the left to right Micrometer Knob so the numeric value is decreasing will move the nozzle tip to the right. After the nozzle is centered on the weld rollers, tighten down the left to right Lockdown Knob.
- Up and down nozzle position, check this by engaging the Drive Foot Pedal and watch the tip of nozzle. It should be pointing at the pinch point of the two weld rollers, if so move on to next alignment step. If not locate the Height Lockdown Knob and loosen by two turns. This will allow us to adjust the Height Micrometer Knob. The Height Micrometer Knob is located at the bottom of the heat system pointing downward. Rotating the Height Micrometer Knob so the numeric value is increasing will raise the nozzle tip. Rotating the Height Micrometer Knob so the numeric value is decreasing will lower the nozzle tip. After the nozzle is aligned, tighten down the Height Lockdown Knob.
Note: Nozzle tip will move up or down when heat is changed. After a heat change of more than 100 degrees, be sure to check height of nozzle tip. - Depth of your nozzle should be at approximately ¼ - ½ of an inch from the pinch point of your weld rollers. Check this by engaging the Drive Foot Pedal and watch the tip of nozzle. If the nozzle is aligned, perform a test weld. If not locate the Depth Lockdown Knob and loosen by two turns. This will allow us to adjust the Depth Micrometer Knob. The Depth Micrometer Knob is located on the back of the heat system facing the direction of fabric flow. Rotating the Depth Micrometer Knob so the numeric value is increasing will move the nozzle tip closer to the weld rollers. Rotating the Depth Micrometer Knob so the numeric value is decreasing will move the nozzle tip away from the weld rollers. After nozzle is aligned, tighten down the Depth Micrometer Knob. When the nozzle is aligned, perform a test weld.
Puller Adjustments
- With the table assembly in place, adjust the height of the material puller by using the steel collar and lock nut to achieve the desired height of the material puller.
- For most applications the material puller wheel should first be adjusted until it is slightly touching the stainless steel roller.
- Next adjust the puller wheel slightly lower by turning the adjusting collar one half turn counterclockwise. This will ensure full contact of the mating surfaces.
Installing/Removing/Adjusting Table Assembly
- Begin by loosening the two black knobs to the right of the operator (removal of these knobs is not necessary).
- Next go around to the puller side of the machine. Just beneath the material puller there will be two black knobs similar to the fasteners previously loosened. Remove these knobs while supporting the weight of the table assembly.
- Lastly, lift up and pull the table assembly out of the throat of the machine through the backside (puller side).
Hot Wedge Heat System Adjustments
A note before beginning; the wedge should be a bit loose (3/16 inch of play). Begin by setting the Master Speed to zero and closing the weld rollers.
First Alignment Step
When the wedge arm swings in and drives forward, it is imperative that the point of the Alignment Pin fits into the Recess of the wedge arm. Check this by engaging the Drive Foot Pedal. If this is OK, move on to the second alignment step. If not, locate the Centric Adjustment Knob on top of the wedge arm. By loosening the Centric Adjustment Knob, you will be able to rotate the Knurled Shaft by ¼ turns until the Alignment Pin fits into the Recess. Tighten the Centric Adjustment Knob when proper alignment is achieved.
Second Alignment Step
The tip of the wedge must be the same height as the pinch point of the weld rollers. Check this by engaging the Drive Foot Pedal and watching the tip of the wedge. It should drive straight to the pinch point of the weld rollers without touching the top or bottom weld roller first. At the same time, the tilt of the wedge needs checked. Ensure that the left tip is not placed higher or lower than the right tip. You must inspect this by getting eye level with the weld rollers. If these are OK, move on to the third alignment step. If not, locate the Height Lockdown knob and loosen by two turns. This will allow adjustment of the Height Micrometer Knob. Rotating the Height Micrometer Knob so the numeric value is increasing, will raise the wedge. Rotating the Height Micrometer Knob so the numeric value is decreasing will lower the wedge. Adjusting the tilt requires a combination of loosening and tightening the Left Tilt Knob and the Right Tilt Knob. After the wedge tip height and tilt is aligned, tighten down the Height Lockdown Knob.
Third Alignment Step
The tip of the wedge must be aligned left to right, and centered on the rollers. Check this by engaging the Drive Foot Pedal and watching to see if the tip is centered on the rollers after it drives forward. If this is alright, move on to the Fourth Alignment Step. If not, locate the Left/Right Lockdown Knob and loosen by two turns. This will allow the adjustment of the Left/Right Micrometer Knob. Rotate to decrease the numeric value on the Left/Right Micrometer Knob will move the wedge to the right. Rotate to increase the numeric value on the Left/Right Micrometer Knob will move the wedge to the left. After the wedge tip is aligned left to right with the weld rollers, tighten down the Left/Right Lockdown Knob.
Fourth Alignment Step
The tip of the wedge must be squared to the weld rollers. Check this by engaging Drive Foot Pedal and looking over the top face of the wedge. See that the wedge squares evenly with the weld rollers. If this is aligned properly, move on to the Fifth Alignment Step. If not, slightly loosen the Wedge Mounting Bolts, very slightly rotate the entire heat system in the desired direction and retighten the Wedge Mounting Bolts. Check the wedge squareness again. Keep repeating until the Wedge is mounted square.
Fifth Alignment Step
The last step involves the wedge depth. Check this adjustment by engaging the Drive Foot Pedal to check the contact between the wedge and the weld rollers. Not enough contact, and the wedge will barley touch the rollers. This will cause there to be a lack of heat transfer through to the material. Too much contact, the wedge will come into contact with the rollers and the upper swing unit of the wedge will deflect. This will cause the wedge to be sucked in by the weld rollers during seaming. If aligned properly, turn the heat switch on and set up for a test weld. If not, locate the Depth Lockdown Knob and loosen by two turns. This will allow for the adjustment of the Depth Micrometer Knob. Rotating the Depth Micrometer Knob to increase the numeric value will move the wedge back away from the weld rollers. Rotating the Depth Micrometer Knob to decrease the numeric value will move the wedge towards the weld rollers. When aligned properly, tighten down the Depth Lockdown Knob. Turn the Heat Switch on and set up for a test weld.
Upper Weld Roller Speed Adjustments
The T300 has an Upper Weld Roller Speed adjustment that allows you to vary the synchronization of the upper weld roller to the lower weld roller. There will be situations that occur where the upper roller will need to rotate at a faster rate then the lower roller. Some examples would be; welding a hem, welding a pole pocket, and welding a straight piece to a radius piece. To increase the speed of the upper roller, follow these steps:
- Press the menu button in the Main Screen.
- Press the welding functions button in the Menu Screen.
To adjust the Upper Weld Roller Speed percentage, you can push the up or down arrows to increase or decrease the speed, or press the box with the percentage and a numeric key pad will appear. Select the numeric value desired.
Inboard Puller Adjustment
- With the table assembly in place, adjust the height of the material puller by using the air cylinder shaft and lock nut. (Pictured).
- For most applications the material puller wheels should be adjusted until they are slightly touching the stainless steel roller.
- Be sure to adjust each side evenly. As adjusting one side will slightly affect the other side.
9.0 Transportation Specs and Storage
Warning! It is recommended to use a forklift when moving or removing a crated machine from a pallet.
Transporting Within a Production Facility
Due to the weight of the Miller Weldmaster machine, the manufacturer requires a forklift or tow motor to be used. The forks are to be inserted below the bottom frame along the center of gravity. Lift slowly to ensure proper placement of forks.
Transporting Outside Production Facility
The manufacturer requires the Miller Weldmaster machine to be placed on a pallet and loaded into a truck using a forklift or tow motor. The forks are to be inserted below the bottom frame along the center of gravity. Secure the machine to the pallet and protect the various controls and features by crating the machine.
Storage
The manufacturer recommends that any time the machine is not in use, it must be protected from excess dust and moisture. The operator should familiarize themselves with the warning symbols on the machine to be alert to the potentially hazardous areas on the machine.
NOTE: The manufacturer will not be held liable for any damage or injuries occurring from any inappropriate use of this machine.
10.0 Technical Requirements
Technical Requirements
- Total air pressure should be 120 psi (8.3 bar).
- The pressure of the Upper Unit Weld Wheel should be between 5 psi and 60 psi (.3 bar and 4.1 bar).
- The lifting of the Upper Weld Roller must be smooth and free, without obvious vibration.
- When the Upper/Lower Weld Rollers are aligned properly, the edges of the two rollers should be parallel and aligned.
- Heat System Swing: The swing in/out of the heat system should be smooth and natural at moderate speed.
- Air lines and air fittings should be free of leaks.
NOTE: Changes in factors such as thickness of materials, qualifications of the operators and different environment and weather may directly affect the product. The operator should be able to understand the following adjustable factors particularly:
- Heating Temperature
- Air Pressure
- The pressure of the Upper Weld Roller
- Air volume
- Placement of heating system
11.0 Additional Machine Documents