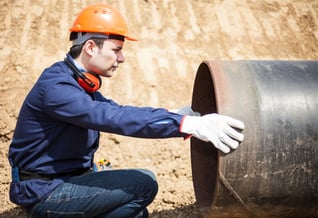
Cost-Effective CIPP Production
With Miller Weldmaster machinery, you have the ability to produce cured in place pipeline (CIPP) consistently and efficiently through automatic operation saving time. The roll production continuous operation contributes to maintaining continuous production, saving time, and improving quality. Customers use our welding and sewing machines to make cured in place pipeline or rehabilitation tubes and calibration tubes for a variety of applications, including sanitary and storm sewers and industrial pipelines.
Weld, Sew or Both
The versatility of our machines means you can weld, sew, or do both. They can automatically inline simultaneously weld or sew two layers of fabric at the same time, enhancing efficiency and quality. This double layer welding capability ensures consistent results and improves the quality of the manufactured products. You can produce both a single-layer, double-layer, or multi-layer pipeline. The machine can handle two layers of fabric simultaneously, ensuring time-saving and quality improvements. Specifically, it can manage one layer of non-woven felt on the inside and one layer of coated felt on the outside. Our customizable machines also excel in cured-in-place pipeline manufacturing, handling both single and double-layer operations with various materials, ensuring an effective product with a watertight seal. Our customizable machines also can apply tape on the top and bottom of sewed seams, to make them waterproof.
In-House Production
Producing your own CIPP lining, including cipp tubes, can be a cost-effective alternative to purchasing liner. The use of coated felt in the manufacturing process ensures a seamless and efficient production of cured-in-place pipelines. Additionally, incorporating a coated felt layer, which can be enhanced with materials like PVC or polyurethane, significantly enhances the efficiency and quality of the production process.
Top Benefits Of Our CIPP Machines:
- Strong and secure seams
- Faster production rates
- Material handling for multiple rolls
- Pallet stacking for improved efficiency
- Fully automated welding for enhanced efficiency, consistency, and quality
- Saving time improving consistency in the manufacturing process
- Tack welds layers to create durable rehabilitation tubes
“Humphrys has been extremely satisfied with Weldmaster’s ability to make us custom heat seaming machinery that has improved our productivity and reduced our labor costs. We consider the purchases of our various Weldmaster equipment a cost saving investment in our future growth.” -Humphrys
Let us help you choose or build the right machine for your application. Contact us to discuss today.