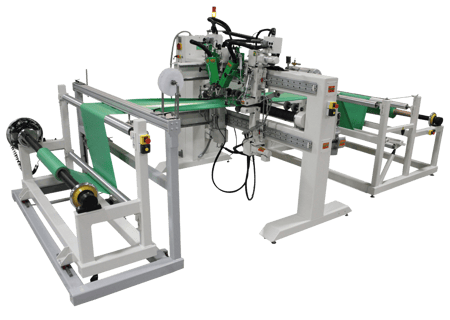
Automated welding machines have revolutionized the manufacturing process of awnings, shade sails, and other textile products. These advanced machines are designed to deliver high-quality welds, significantly increase efficiency, and reduce labor costs. With the capability to handle a variety of materials, including PVC, acrylic, and polyester fabrics, automated welding machines have become indispensable tools for businesses in the awning and shade sail industry. By automating the welding process, these machines ensure consistent, strong welds that enhance the durability and aesthetic appeal of the final products. Whether you’re producing residential or commercial-grade awnings, shade sails, or screens, automated welding machines offer the versatility and reliability needed to meet the demands of modern manufacturing.
Automate Your Awnings, Screens & Shades
Automated solutions for the manufacturing of awnings, canopies, screens and shades are used to produce top quality residential or commercial grade products. These fully automated solutions will provide a faster and more efficient process resulting in less production costs to you. These solutions are also ideal for manufacturing roller blinds, ensuring precision and durability in the final product.
Welding motorized or retractable awnings provide product longevity and offer a leakproof product. Welding heats in-between the two layers of fabric eliminating the needle punches from sewing and provides a more aesthetically pleasing seam to your customers.
Automated welding solutions also provide:
- Versatility to accommodate multiple applications
- High-speed production for increased output
- Customization by applying keder, weld overlaps, hems, pockets, rope and hem, cut to length, and more
- Ability to weld multiple rolls of same or different thickness together at one time
Each solution is fully customizable and can incorporate several different options including, welding, unwinds, keder applications, multiple stations, grommets and more… Each solution can be built to meet your needs today and also grow with you throughout the years.
Acrylic and PVC materials can be welded with hot wedge, hot air, impulse and radio frequency welding or glue for full versatility.
Still have questions? Contact one of our automated specialist to discuss your production and potential options.
Miller Weldmaster will help you select the right solution for your application.
Types of Automated Welding Equipment
There are several types of automated welding equipment available, each designed to meet specific welding needs. Understanding the unique capabilities of each type can help businesses choose the right equipment for their applications:
- Impulse Welders: These machines use a high-frequency electrical impulse to generate heat, creating a strong weld. They are ideal for materials that require precise temperature control and are commonly used for welding delicate fabrics and thin materials.
- Hot Air Welders: Utilizing a stream of hot air to melt and fuse thermoplastic materials, hot air welders are perfect for applications involving PVC and other thermoplastics. They provide a robust and durable weld, making them suitable for heavy-duty applications.
- Ultrasonic Welders: These machines employ high-frequency vibrations to generate heat, resulting in a clean and strong weld. Ultrasonic welders are particularly effective for materials that require a seamless finish, such as polyester and other synthetic fabrics.
- Robotic Welders: Equipped with a robotic arm, these machines automate the welding process with high precision and accuracy. Robotic welders are ideal for large-scale production environments where consistency and speed are crucial.
By selecting the appropriate type of welding equipment, businesses can ensure they achieve the desired weld quality and efficiency for their specific applications.
Applications and Features
Automated welding machines are utilized across various industries, including construction, manufacturing, and automotive. These machines are equipped with features designed to enhance efficiency and precision, making them invaluable assets in the production process:
- Automatic Temperature Control: This feature allows for precise control over the welding temperature, ensuring a strong and consistent weld. It is particularly useful for materials that require specific temperature settings to achieve optimal results.
- Material Handling Systems: These systems enable the machine to handle and position the material with ease, reducing labor costs and increasing efficiency. Automated material handling ensures that the fabric or material is correctly aligned and tensioned, resulting in a high-quality weld.
- Welding Speed Control: Adjustable welding speeds allow the machine to accommodate different materials and applications. This feature ensures that the welding process is optimized for each specific material, enhancing the overall quality and efficiency of the production.
By incorporating these advanced features, automated welding machines provide businesses with the tools needed to produce high-quality products efficiently and cost-effectively.
Materials and Advantages
Automated welding machines are capable of handling a wide range of materials, including metals, plastics, and fabrics. The advantages of using an automated welding machine are numerous and can significantly impact the production process:
- Consistent Output: Automated welding machines provide consistent welds, reducing the risk of human error. This consistency ensures that each product meets the required quality standards, enhancing the overall reliability of the final product.
- Reduced Labor Costs: By automating the welding process, these machines can operate continuously, reducing the need for manual labor. This reduction in labor costs can lead to significant savings for businesses, allowing them to allocate resources more efficiently.
- Increased Efficiency: Automated welding machines can produce high-quality welds at a faster rate than manual welding methods. This increased efficiency allows businesses to meet higher production demands and reduce lead times.
- Improved Productivity: With the ability to handle large volumes of material, automated welding machines can significantly increase productivity. This capability enables businesses to scale their operations and meet the growing demands of their customers.
By leveraging the advantages of automated welding machines, businesses can enhance their production capabilities, reduce costs, and improve the overall quality of their products.
Choosing the Right Machine
Selecting the appropriate automated welding equipment is crucial for achieving optimal results. Businesses must consider several factors to ensure they choose the right machine for their specific needs:
- Material Type: Different materials require different welding techniques and machines. It is essential to select a machine that is compatible with the materials being used to ensure a strong and durable weld.
- Weld Strength: The machine must be able to produce a weld that meets the required strength and durability standards. This consideration is particularly important for applications where the weld will be subjected to significant stress or environmental conditions.
- Operational Complexity: The machine should be easy to operate and maintain, reducing downtime and increasing productivity. User-friendly machines with intuitive controls can help businesses streamline their operations and minimize training requirements.
- Budget: Businesses must consider their budget and choose a machine that meets their needs while staying within their financial constraints. It is important to balance the initial investment with the long-term benefits of the machine, such as increased efficiency and reduced labor costs.
By carefully evaluating these factors, businesses can select the right automated welding machine for their needs, enhancing efficiency, productivity, and profitability.