This instruction manual is intended to be a guide when operating the Boxmat PRO INTELIGO. To ensure optimal performance from your welder, please follow the recommendations and specifications precisely.
Table of Contents
- Chapter 1: Introduction
- Chapter 2: Health and Safety Regulations
- Chapter 3: Technical Data
- Chapter 4: Technical Specifications
- Chapter 5: Installation
- Chapter 6: Machine Operation
- Chapter 7: Description of HMI Panel Screen
- Chapter 8: Maintenance
- Chapter 9: Occupational and Safety Rules
- Chapter 10: Electrical Documentation
- Chapter 11: Pneumatic Documentation
- Chapter 12: Utilization and Machine Breaking
- Chapter 13: Enclosures
- Chapter 14: Additional Machine Documents
For more technical information regarding this machine call our Resolution Center at 1-855-888-WELD or email service@weldmaster.com.
1.0 Introduction
Boxmat PRO is the most modern and most versatile machine on the market and revolutionizes the production of corrugated packaging. Thanks to the automatic and tool-free change of settings on the HMI touch panel which can be changed within a few seconds, any product size may be programmed in standard, FEFCO types. PRO is ideal for the production of short series as well as for large, mass production. Slot-cutting, the removal of excess material, scoring, the removal of tongues of adhesive, as well as cutting the format to size, is carried out in one cycle without the need for additional attachment.
In ‘one go’, boxes of 3/5 layers of corrugated cardboard can be made. More than one box can be made from a suitably large format in just a single cycle.
The positions of the longitudinal tools are set using servo drives depending on the required size and thickness of the cardboard. Formats are centrally positioned for automatically positioned bumpers. A set of non-slip rollers and input-output shafts ensures precise and stable carton guidance throughout the entire cycle.
The innovative system applied, using circular knives, allows excess, or waste cardboard to be cut off from the remainder of the sheet. This solution facilitates the bi-directional correction of the size of the sheets and enables the sheets currently in production, to be cut to different sizes simultaneously, without having to be cut on a separate, peripheral device.
FEATURES:
- Notching, bi-directional scoring and cutting off waste in one cycle
- One integrated module for cutting, scoring and cutting off, eliminates production errors in multi-module machines
- Quick change of machine settings, on the touch panel, thanks to servo drives
- Possibility of longitudinal scoring which is a scoring function, transverse scoring and cutting sheets into smaller pieces - a crevice tool
- 4 knives + 4 longitudinal scoring wheels adjustable on the panel - a standard option
- An integrated punching system for cutting holes
- Ecological power and drive system as well as low power consumption
- Selection of styles, sizes, functions and the depths of the scores, using the touch screen
- Cardboard feeder with a reliable pick-up system
- Vibro-insulating legs preventing transmission of vibrations
- Secure and fast remote machine calibration and updating, thanks to remote internet connection
- Easy exchange of scoring wheels and cutting blades
ATTENTION: Any intention of using this machine for any purpose other than as described in this manual must always be discussed with the manufacturer.
ATTENTION: For the safety of all operators and other personnel, it is important that this manual is read and understood by all personnel; all instructions should be followed.
ATTENTION: It is highly recommended that each operator, once trained to use this machine, should append their name and signature to the form in this manual.
ATTENTION: This machine was designed for use by able-bodied operators. Please contact the manufacturer for help and advice if it needs to be adjusted or modified for others.
2.0 Health and Safety Regulations, Signs and Labels
The health and safety of operators and of other personnel within the vicinity of this machine, is of paramount importance.
In order to use this machine safely, it is very important that this manual is read thoroughly by all personnel who intent to work with, or near the machine. All safety instructions should be adhered to, including the warning labels in the manual, as well as those displayed on the machine.
It is imperative that the purchaser be obliged to work out their own WORKSTATION INSTRUCTIONS for their machine operators, using the instructions in this service manual and the knowledge derived from the manufacturer's own experience of the technology of the product.
The ultimate, legal and financial responsibilities for all the potential events that may occur, due either to ignorance of this service manual or ignorance of Occupational Health and Safety regulations, lies with the purchaser. It is, therefore, ESSENTIAL to read and follow the safety instructions.
Warning Signs
ATTENTION: Each operator MUST read the text of this service manual before undertaking any work with the machine.
ATTENTION: The purchaser is strongly advised to draw up their own WORKSTATION INSTRUCTIONS for the machine operators, on the basis of the text included in this service manual and the knowledge derived from their own production technology.
ATTENTION: UNDER NO CIRCUMSTANCES should the machine be operated by unqualified personnel. Machine operators must be familiar with Occupational Health and Safety regulations with special focus on the risks inherent in this machine. As a consequence of the aforesaid, documentation, approving completion of training and signed by the trained operator, should be issued.
ATTENTION: The machine was not designed to be operated by disabled operators. If the need arises - and after prior consultation with the Manufacturer- the machine can be appropriately adjusted for disabled operators.
ATTENTION: According to the manufacturer's recommendations, the machine should be installed in an industrial environment only.
ATTENTION: Careless handling of the machine, during transport and/or relocation, may lead to severe injury or accidents.
ATTENTION: Periodical, adequate preventive inspection of the fire protection system should be carried out, in and around the machine. The purchaser is fully responsible for arranging to conduct such inspections.
ATTENTION: A life threatening, high-power network voltage of 3 x 480V; 50...60 Hz is supplied to the machine. As a result, all servicing should be undertaken by appropriately qualified personnel only, as required by law.
ATTENTION: Work carried out in the feeding, cutting or bending zones within the systems, should be conducted by qualified personnel only, after taking all precautionary measures. In the above-mentioned zones, higher instances of potential body injury are possible.
ATTENTION: The EMERGENCY STOP button is designed to be pressed at any time but especially when an emergency shutdown is urgently needed.
ATTENTION: The area surrounding the machine should not be blocked by any objects, as this may result in personnel stumbling, sliding and falling which may lead to severe injury.
ATTENTION: The operator should always ensure that all doors, lids, shields and other protective devices are securely in place before the machine is started.
ATTENTION: An operator must never climb onto the machine when it is in operation.
ATTENTION: The through-route of the corrugated board must NEVER be blocked by personnel or by any obstacle.
Prohibitory and Mandatory Signs
UNDER NO CIRCUMSTANCES should the machine be operated by untrained personnel. The machine’s operators must be familiar with Occupational Health and Safety regulations with special focus on the risks inherent in this machine.
ATTENTION: UNDER NO CIRCUMSTANCES should the machine be operated by unqualified personnel. Machine operators must be familiar with Occupational Health and Safety regulations.
UNDER NO CIRCUMSTANCES should the machine be assembled, dismantled or transported by untrained personnel, nor by those unfamiliar with the safety regulations included in this service manual, since such activities may lead to an accident or to financial loss.
UNDER NO CIRCUMSTANCES should servicing or maintenance be conducted, or preventive measures be taken, without fully disconnecting from the electrical supply.
UNDER NO CIRCUMSTANCES should any of the sub- assemblies, such as the guide rollers, the cutting or scoring tools, be touched.
UNDER NO CIRCUMSTANCES should any measures be undertaken which could lead to a reduction in the machine’s safety status; this includes such measures as blocking master switches, removing guards or disconnecting sensors, etc.
UNDER NO CIRCUMSTANCES should an operator climb onto the machine during the loading procedure or during its regular work cycle.
UNDER NO CIRCUMSTANCES should any potential fire, near the machine, be extinguished with water. Use only licensed, sophisticated, firefighting agents and fire-hazard protection products.
UNDER NO CIRCUMSTANCES should the guards be removed during the machine’s work cycle.
UNDER NO CIRCUMSTANCES should the machine be sprayed with water during its regular work cycle or when it is idle.
UNDER NO CIRCUMSTANCES should any maintenance tasks be conducted while the machine is in operation.
UNDER NO CIRCUMSTANCES should any oil, solvent or any other caustic or toxic substances be poured out, either in or near the machine.
UNDER NO CIRCUMSTANCES should mobile phones be used in the immediate vicinity of the machine.
UNDER NO CIRCUMSTANCES should any naked flame be used in the immediate vicinity of the machine.
UNDER NO CIRCUMSTANCES should cigarettes be smoked in the immediate vicinity of the machine.
UNDER NO CIRCUMSTANCES should alcohol be drunk in the immediate vicinity of the machine, nor should personnel, under the influence of alcohol, operate the machine.
UNDER NO CIRCUMSTANCES should personnel eat in the immediate vicinity of the machine.
IT IS STRONGLY ADVISED that each person, assigned to operate the machine, be fully trained. The scope of training should cover operation of the machine, as well as Occupational Health and Safety regulations, with special focus on the risks inherent in the machine.
IT IS HIGHLY RECOMMENDED that ALL covers and guards, designed for the machine, be used.
IT IS ESSENTIAL that in the event of any accident involving the operator, or any machine failure, both should be reported to the management promptly.
IT IS ESSENTIAL to wear safe, close-fitting, workwear to reduce the possibility of being snagged or pulled into the machine.
IT IS ESSENTIAL to wear protective gloves while operating the machine.
IT IS ESSENTIAL to wear anti-slip working footwear.
Hearing protection must be worn in this area.
IT IS ESSENTIAL that long hair be tied back in such a way as to reduce the risk of being snagged or pulled into the machine; operators must wear either appropriate hair covering or wear their hair tied up.
IT IS ESSENTIAL to keep the floor around the machine clean and clear of any paper, board or other waste.
IT IS REQUIRED that all machine operators are well-trained personnel, acquainted with Occupational Health and Safety regulations; they should also be familiar with all hazardous situations likely to occur in the operation of sophisticated machines of this complexity.
IT IS ESSENTIAL to use the emergency stop switch button whenever the operator's life or health is at risk.
IT IS ESSENTIAL to disconnect the machine from the power supply whenever servicing, maintenance or preventive activities are underway.
During packing, unpacking and transportation, special measures should be taken, in order to prevent the machine from tipping over.
Type |
Boxmat PRO INTELIGO |
Material |
single, double up to 1/4”, up to 1050 g/m2 |
Power supply |
3 x 230 VAC; 50/60 Hz |
Control voltage |
24 VDC |
Installed power |
5.5 kW |
Working pressure in pneumatic system |
0.6 – 0.8 MPa |
Filtration accuracy [(FR [filter reducer] system) |
20 μм |
Demanded class of working medium activity in pneumatic system |
4-4-4 according to ISO8573-1 standards |
Efficiency |
up to 600 sheets per hour |
Carton’s styles |
40 pre-set FEFCO styles + free style |
Recipe memory |
1000 items for FEFCO + 1000 items for freestyle |
Maximum board size |
94” width x 300” length (single sheet) |
Minimum board size |
10” width x 25 ½“ length |
Distance between slotting knives |
2 ¾“ – 78 ¾“ (with 8” knives) |
Width of slot |
5/16“ |
Minimum panel size |
¾” |
Glue flap |
option to choose the length of the flap |
Machine dimensions |
134” x 63” x 63” (L x W x H) |
Weight |
2800 kg (6200 lbs) |
4.0 Technical Specifications
- The Boxmat Pro machine consists of the main body, containing all the electrical and mechanical components, and movable work table. The main body is based on a metal frame ensuring the adequate level of stability. The work table is designed to assist the operators feeding the corrugated material through the machine.
- The corrugated blanks are carried through the machine by a series of rollers and wheels driven by servo-drives. In a similar way the slotting beam is propelled by a servo drives.
- Behind the slotting/scoring beam is the innovative system of rotary tools that enable the operator to cut off excess board and eject them without any cuts or scores enabling them to be re-used for smaller boxes. This also allows oversized blanks to be trimmed to size as they pass through the machine instead of having to trim on another, separate machine.
- It also allows the production of two boxes at one time (with Multi-production option), if box size and sheet size are suitable by attaching a central knife.
- The slots are punched out by a system of blades attached to the scoring beam.
- The slotting blades are automatically moved to the correct positions by asynchronous motors driven by the inverter and encoder, once the dimensions is entered into the touch screen.
- The left hand guide is positioned automatically and, once a board blank is positioned against it, the right hand guide can be slid up to it to allow the blank to pass through the machine without any twisting.
- The machine is equipped with a full set of covers and guards to protect operators from the moving blades and knives. To comply with all European safety regulations, the machine will not operate if these are not all in place and an appropriate error message will be displayed on the screen.
The manufacturer will ensure that the machine is appropriately packaged for transport. The type and strength of packaging are adapted to the distance and means of transport used, as well with regard to the potential risks associated with the means of transport used. The Manufacturer suggests that Recipients use the Manufacturer's means of transport and service personnel.
Storage of an unused machine does not imply any requirements other than a suitable storage environment. Warehousing must provide sufficient protection against atmospheric agents and be dry, with an acceptable humidity level below 70%. The storage temperature should be between 5 ºC and 40 ºC.
Adequate anti-corrosion protection should be ensured, especially for metal parts which, for technical reasons, have not been painted or protected against corrosion.
If the machine is delivered in a crate and/or covered with film-wrap that creates an anti-corrosive atmosphere, the machine should remain in the same, throughout the entire storage period.
To protect against moisture, it is recommended that the machine is not stored on the floor of the warehouse but on pallets, in order to keep it lifted off the floor.
This box maker should be stored vertically in a dry and well ventilated room. The machine is sensitive to vibration, shock, violent jolts and long-lasting tilts. Even if it is dropped from a relatively insignificant height this may lead to its permanent and irreversible damage.
The above provisions are intended to make all persons and services, who have contact with this device, aware of its high sensitivity to any impactful stimuli and, at the same time, aware also, that no claims, arising from such permanent damage, as described above, will be considered as a valid complaint.
For further advice or information, please contact the manufacturer’s service technicians.
Transport
UNDER NO CIRCUMSTANCES should the machine be assembled, dismantled or transported in any way by unqualified personnel or those unfamiliar with the safety and care information included in this manual. Failure to comply with this basic rule may lead to accidental damage or injury not covered by the manufacturer’s warranty or liability.
- The entity responsible for transporting and installing the machine at the Ordering Party's plant should be determined at the contract signing stage, however at the latest, after the technical acceptance of the machine at the Manufacturer's plant and before being issued to the Ordering Party.
- Due to the nature of the device, the Manufacturer suggests that the Recipients use the Manufacturer's means of transport and service personnel.
- The machine should be moved using lifting devices such as cranes, forklift trucks or pallet trucks, all of which should have sufficient lifting capacity for the purpose of safe transportation. The persons operating them should have the required permits and the training, as required by law.
- The correct mode of transportation for BOXMAT PRO machines is presented below.
Fig. 2. The location for lifting the machine is indicated by the pictogram (Fig. 2 -1)
Fig. 3. The correct transportation of the machine using a forklift truck
It is forbidden to lift the BOXMAT PRO machine where so indicated by pictograms; the drawing below refers.
Fig. 4. It is forbidden to lift the BOXMAT PRO machine by its side walls, using a forklift truck.
ATTENTION: Failure to comply with the above pictograms and methods of assembly, may result in damage to the machine's structure and components.
ATTENTION: Machine must be transported vertically.
It is essential that the machine, and all parts and accessories, must be packaged safely and securely. Suitable protective wrapping, pallets and/or crates should be supplied to ensure that the machine and all peripheral parts and accessories arrive for installation safely and undamaged. It is strongly advised to allow the manufacturer to undertake all these tasks to ensure a safe and efficient delivery and installation.
As far as transport procedure is concerned the machine's weight (c. 2800 kg - 6200 lb.) must be taken into account.
ATTENTION: Careless handling of the machine during transport and/or relocation may lead to severe accidents or injuries.
Installation
Installation of the machine at the workplace, is effected by the Ordering Party's personnel, once the contents of these operating instructions and the Manufacturer's services have become familiar to- and have been agreed to- by the Ordering Party’s personnel. The correct setting of the printer is important as a precondition for its optimal functioning and for the comfort and safety of the operators.
Preparation of the location for the machine, the availability and parameters of electrical, pneumatic and ventilation connections, as well as the preparation of the specific design and acceptance requirements, needed to facilitate operation of the machine, is the responsibility of the Ordering Party.
The Manufacturer will provide the necessary guidance and information to assist the Ordering Party in this regard.
After delivering the machine to its designated location, it should be unpacked and leveled. Its technical condition should then be checked and any damage caused in transport, should be rectified.
ATTENTION: The floor on which the machine is to be placed must have sufficient structural strength to support the weight of the machine and any vibration generated by the normal process of manufacturing boxes. It should also be noted that the majority of the weight of the machine is concentrated at the feet.
ATTENTION: Once the machine is leveled it should not be moved without repeating the leveling process.
The most optimal flooring is made of plain concrete of sufficient depth and coated with a thin layer of non-conducting material.
The foundation on which the machine is placed should be architecturally compliant with the building standards and safety rules fulfilling the requirements of depth, strength and level.
The Buyer is the only person responsible for preparation of base on which the machine is supposed to be installed.
ATTENTION: If the assembly and set-up procedures are conducted individually by the purchaser, they should be performed due to the instructions included in this service manual and/or according to the instructions provided by the manufacturer during the technical acceptance procedure.
Use the screws in the machine feet to level the frame. (The sides of the machine's body are the reference plane for level).
ATTENTION: After each change position the machine, check the gap between the upper and lower slotting knives. On the entire length of the upper slotting blades, from the front and back side, the gap should not be less than 0.004 inch.
When the machine is leveled, then the work tables should be assembled and placed at the front and rear of the machine (tables are available on demand). Once both work tables are delivered, they should be leveled to the machine.
Work Conditions
GENERAL INFORMATION
ATTENTION: It is the manufacturer’s recommendation, that the machine should be installed in an industrial environment only.
As written and described within this technical manual, this machine has been designed and manufactured to be used in an industrial environment for the conversion of corrugated fiberboard into a range of cartons and, as such, this machine must be operated within the health and safety regulations associated with the industrial box-making environment.
This machine must not be operated in a potentially explosive atmosphere, in an atmosphere with a high level of pollution, high humidity, high temperatures or in aggressive, or corrosive, fumes.
Due to the electronics and sensors within this machine, it should be used in temperatures from +15°C to +35°C and in a relative humidity ranging from 35% to 85%. Atmospheric humidity condensation, or any potentially aggressive agents, should be avoided.
Temperature changes within the operating environment should not exceed 10°C and the relative humidity should not vary by more than 10%.
ATTENTION: If there are significant temperature and humidity differences between the delivery process and the installation site, the machine should be stored and acclimatized in the site where it is to be operated for 24 hours before starting up.
LIGHTING
The criterion for the minimum level of lighting indicates that the acceptable lighting on a horizontal working plane, in rooms where personnel attend for a long time, regardless of what visual tasks are performed, should be 300 lx.
Where, however, there is a degree of visual difficulty greater than average, resulting in difficulties in working, the requirement pertains to ensure higher viewing comfort; this also applies where employees are mostly people over 40 years of age. With this in mind, the level of intensity in the lighting should then be higher than the minimum permissible level of 500 lx.
5.4.3. NOISE
The device is the source of the noise intensity above 85dB requiring use of plant protection personnel.
Hearing protection must be worn in this area!
We note that all environment have their own noise emissions, which can effectively influence the levels of noise issued by the machine during operation, especially in various technological systems.
Power Supply Parameters
ELECTRIC SUPPLY
The machine must be connected to a power supply of 3 x 480 VAC; 50/60 Hz; (3P+N+PE), equipped with overcurrent protection.
The Buyer's installation must provide shock protection in accordance with PN-EN 60204-1:2018-12.
COMPRESSED-AIR SYSTEM
The machine uses air pressure ranging from 6-8bar / 85-110 psi.
The filtered impurities are less than 20 µm, to comply with ISO8573-1 4-4-4 standards.
6.0 Machine Operation
Assuming that all conditions for the installation and activities described in the previous chapter have been met and successfully carried out, preparations can begin for the first start-up of the machine, in production conditions at the Contracting Party's plant.
Assuming that all conditions for the installation and activities described in the previous chapter have been met and successfully carried out, preparations can begin for the first start-up of the machine, in production conditions at the Contracting Party's plant.
ATTENTION: Initially, the machine should be started up under the supervision of the manufacturer’s agents.
The Service Conditions must be read and understood before starting the machine.
SERVICE CONDITIONS – GENERAL GUIDELINES AND PROCEDURES
To ensure correct machine operation, all adjustments and settings must be carried out by the manufacturer's trained technicians, once the machine has been assembled and installed and the initial start-up procedures have been implemented. Corrugated material for testing the machine should be made available by the Buyer.
Before using the machine, that is, prior to its first start-up, the Contracting Party has the absolute obligation to train those employees who will be its future operators. Moreover, due to the different work cycles carried out by our machines, in various industrial environments, the Recipient has the absolute obligation to create a clear and transparent workplace instruction manual for the device, adapted to its own production cycles.
UNDER NO CIRCUMSTANCES should the machine be operated by unqualified personnel. The machine operators must be familiar with the occupational health and safety rules, with the focus on giving special consideration to the risk created by using this machine.
ATTENTION: The Recipient, or a person authorized by him/her on the basis of these operating instructions and the characteristics of his/her own production technology, has the absolute obligation to compile a MACHINE-BASED INSTRUCTION MANUAL for the employees.
IT IS STRONGLY RECOMMENDED to instruct each person assigned to work with, or near, this machine not only in the operating of the machine but also in the occupational health and safety rules associated with operating the machine.
The setting and checking procedure, implemented prior to using this machine, must only be performed by trained and authorized personnel.
BEFORE USING THE MACHINE IT IS STRONGLY RECOMMENDED TO CHECK THE FOLLOWING:
- the effectiveness of protection against electric shock;
- the supply voltage;
- value and phase compliance;
- the emergency buttons (safety switches - EMERGENCY STOP) if necessary, unlock by turning clockwise;
- the magnetic safety sensors of the covers and side windows;
- the security locks are, in fact, locked;
ATTENTION: Any maintenance work or changing of tools etc., that requires the machine to be operated with covers open, must only be carried out by trained and competent personnel and must be completed as quickly as possible before the covers are closed and full safety status is restored.
ATTENTION: All switch boxes, covers and guards must be closed before attempting to use the machine and must remain closed during use.
It is strictly forbidden to operate the machine with any safety switches or other safety devices defeated or altered in any way. All these devices are fitted to protect the safety of the operator and other personnel. It is recommended that all such devices are checked and tested regularly to confirm that they are all operating correctly.
Each machine operator should be familiarized with all the safety features and devices associated with this machine.
IT IS STRICTLY FORBIDDEN to remove any covers or guards while the machine is in operation.
IT IS STRONGLY RECOMMENDED TO attach and close ALL covers and guards designed for the machine.
In the area around the machine, and up to 1.5m, all obstacles must be removed and the area must be clean and appropriately lit. Particular care should be taken when Fork Lift Trucks are fetching and removing materials and cartons.
The area in close vicinity to the machine should be clean and cleared of impurities such as oil, dust and dirt in order to reduce to the minimum the risk of a slip, trip or fall.
ATTENTION: When the machine is in operation the area surrounding the machine should not be blocked as it may cause a slip, trip or fall.
UNDER NO CIRCUMSTANCES should any oil, solvents or other caustic or toxic liquids be poured out in the close vicinity to the machine.
IT IS THEREFORE ORDERED to keep the floor around the machine clean and clear.
The machine controls, indicators, flexible conductors, pipes or shafts should not be used as handles. Any unintentional displacement of these machine parts may cause accidental and unintentional activation or changes to the machine working parameters and, in extreme situations, may lead to the machine failure or break- down.
IT IS ESSENTIAL that any accident involving the operator, or any machine failure, should be promptly reported to the management.
The qualified machine operators should be equipped with the regular working clothing, protective gloves and anti-slip, safety footwear.
Since the basic risks to the machine operators are moving rollers, wheels and shafts, the machine should not be operated by personnel wearing loose clothing or long and loose hair.
IT IS ESSENTIAL to wear the suitable working clothing reducing to the minimum the possibility of being snagged or pulled into the machine.
IT IS ESSENTIAL to wear protective gloves while operating the machine and handling cardboard.
IT IS ESSENTIAL to wear anti-slip working footwear.
Hearing protection must be worn in this area!
IT IS ESSENTIAL to secure the operator’s hair in such a way to reduce to the minimum the risk of being snagged or pulled into the machine.
Controls and Indicators Available for Operator
In the machine presented, all handling elements are located directly on its construction body, or on the control panel. Before using the machine, all personnel operating the machine should familiarize themselves with the location of these elements and the functions they control.
The handling and control elements of the machine which are available to the operator include:
Fig.5. MAIN SWITCH Fig.6. CONTROL PANEL Fig. 7 COMPRESSED AIR TERMINAL
- MAIN SWITCH - the switch installed on the switch box doors (Fig.5), is designed to switch the electrical supply on and off. When it is turned to the 1 position it means that the machine is ON, when it is turned to the 0 position, it means that the machine is switched OFF.
- HMI panel – a touch-sensitive screen which can be found on the control panel (Fig.6), it is designed to programming and control the machine.
- START – This green button, when lit, indicates that the machine is ready for work (Fig.6)
- RESET – a blue button used to restart the control system and the machine’s safety system and alarms after an error (Fig.6).
- EMERGENCY STOP - a mushroom-headed button for the immediate shutdown of the entire machine, in the event of any failure or accident. Buttons are located on the operator's panel (Fig.6) and to the rear and side of the machine.
-
Compressed air terminal (Fig.7);
-
The manually operated compressed air shut-off valve (in order to open the valve - turn it to the left and set to ON position; a turn to the right - the OFF position - the valve is closed);
Positioning of Right Guide and Input Stops
ADJUSTING THE POSITION OF THE RIGHT LIMITER AND THE ENTRY BUMPERS
ATTENTION! Regulation should be conducted after selection of style, entering the cardboard dimensions and automatic setting of left guide.
- Place the blank on the table
- Undo handles of the input stops (Fig.9).
- Lift up the input stops gently and slide apart two of them towards the ends of board and the third one should be placed in the center and over the roller (Fig.11).
- Tighten up the orange handles of the input stops (Fig.9).
- Using the knob (Fig. 10) set the gap under each bumper so that it is possible to insert one carton into it; ensure, however, that it is not possible to insert two cartons (Fig.12).
- Set the right stop with the help of the hand grip (Fig.13) so that it almost sticks to the mat; leave 1/16” of slack so that the mats do not jam between the stops (Fig.14).
Connection to a Power Source
- Check the area around the machine. It is designed to work in a clean and neat environment without any waste or obstacles that could adversely influence on its regular working activity.
- Prepare the corrugated blanks, ready for production.
- If required by the production cycle provided by the user, place containers for waste and ready-printed cartons in a suitable place, near the machine.
- Check that all covers and guards are in place and that all doors are closed – it is strictly forbidden to perform work with open covers or missing guards as this will trigger the proximity sensors and prevent the machine from working.
- Check that the EMERGENCY STOP push-button on the control panel is in the correct position. In order to reset it turn the mushroom-headed push- button clockwise.
- Connect the electrical power supply to the machine (put the plug into the power supply socket and/or switch on) and the compressed air system by connecting the air hose to the terminal and switching on the compressor.
- Check that the pneumatic supply is between 85psi/6bar and 110psi/8bar.
- Turn the MAIN SWITCH installed in the machine side casing, to the 1 / ON position.
- PC Panel (HMI) with Windows system will start-up.
-
Due to standard procedure when the machine is switched on, an error message such as “Safety system not ready - press RESET button” should be found on the HMI touch panel. In order to put the machine in motion press RESET button. As a result, the test of safety system and the drives shall be put into operation. When the START button flashes green, it means that the machine enters a stand-by mode and it is ready for work.
-
If all procedures end up successfully, the machine is ready for work – the main window should be displayed on the HMI panel.
Fig. 15. Boxmat interface Inteligo start-up
Fig. 16. Safety system not ready
Fig. 17. Boxmat PRO main screen
ATTENTION: Covers must always be closed or the machine will not work.
ATTENTION: the EMERGENCY STOP button is designed to be pressed at any time especially when an emergency shut- down is promptly needed.
ATTENTION! In case the error message can still be seen on the display after pressing the START button, go to ALARMS, ERROR MESSAGES and FAILURES shown in the technical documentation.
Disconnection
The following switch-off procedure should always be implemented when production is completed:
- Go to main screen
- Shut down the Boxmat interface - choose "Exit" icon
- Shut down the Windows system
- After a proper Windows shut down, turn the MAIN SWITCH to the position 0-OFF -- this means that the machine is switched off.
- Clear the working environment around the machine.
- If the machine is being shut down for a longer period - i.e. the weekend - The electrical power supply and the compressed air should be disconnected.
ATTENTION! Do not turn off the machine during Windows shut down ! This can damage HMI PC !
Fig. 18. Exit from Boxmat interface
Fig. 19. Shut down Windows
7.0 Description of HMI Panel Screen
Home - Choice of Box Design
On the main screen, are the basic formats of the FEFCO styles available. First, select the style or select ‘Other’ if a Free Style box is to be designed.

- SETTINGS - the button opens a SETTINGS screen (page 50). On this screen, three further screens can be selected:
- Manual Movement - options available on the Manual Movements screens which allow all moving parts, available in the machine, to be moved manually.
- Service - options available in the Service screens contain statistical information on the machine’s operation and advanced parameters of the machine's operation.
-
MENU - the button opens a screen showing the following features: LOGGING IN, RECIPES, STATISTIC and LANGUAGE settings.
Choose this button to change language of the interface.
- QUEUE JOB - the button opens screen with "Queue job" work mode.
- FEFCO - the button opens screen with saved FEFCO recipes.
- Box wizard - the button opens screen with saved recipes prepared in Box Wizard.
-
SLOTTED-TYPE BOXES (flap boxes) - the button opens a screen containing templates for flap boxes in FEFCO styles (Fig. 21).
Fig. 21. The Screen displays Flap Box style templates FEFCO 2xx (1/2)
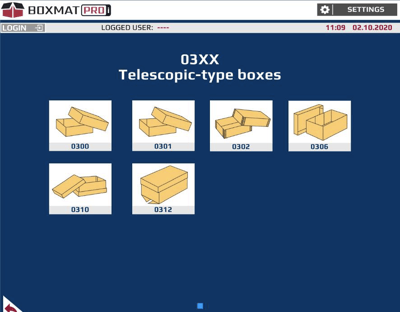
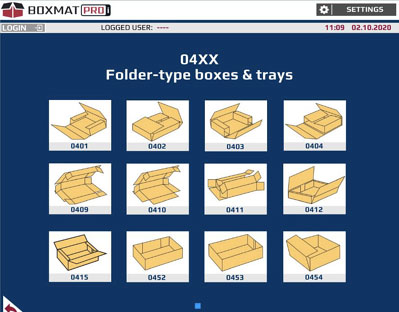
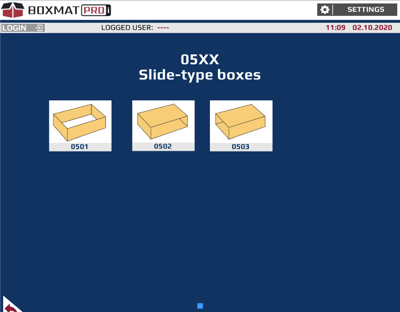
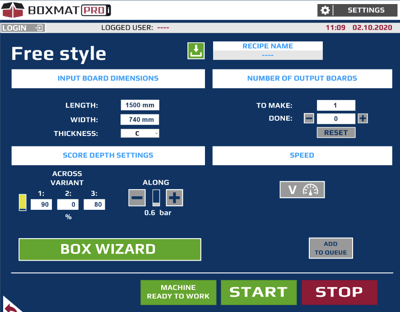
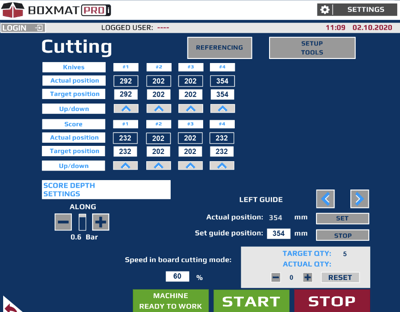
Pressing the SETTINGS button (1) in the main screen, will open the Settings screens.
Options available in Settings allows to manual movements of each tool installed in the machine, setup machine parameters like tools orientation, etc.
With Service access level it is possible to change service parameters - advanced parameters of the machine's operation.
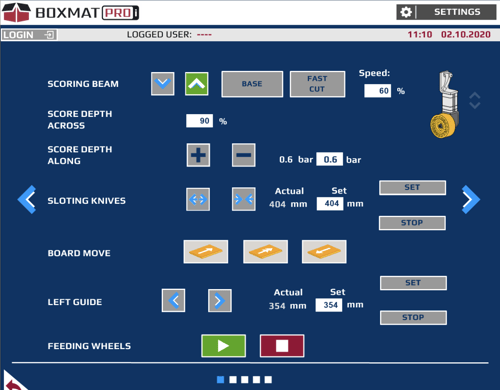
Fig. 27. Manual Movements screen (1/3)

moves the scoring beam upwards
moves the scoring beam downwards;
When the Up Arrow button displays yellow, it indicates that the scoring/slotting beam is in the top position ready for starting.
14. BASE - the button sets the scoring beam with slotting knives in the top position for starting. Reference mode.
15. FAST CUT - the button starts one full cycle of the scoring/slotting beam at setup speed- value 0% - without scoring between the slots;
- value 100% - max scoring depth between the slots;
17. Score depth along - air pressure for scoring wheels
18. + - these buttons change the depth of the scores along the box by adjusting the pressure on the wheels/rolls. Pressing the button changes the pressure setting by 0.1 bar.: • + increases the pressure;
- + increases the pressure;
- - decreases the pressure
It is possible to set pressure within the range 0 to 3 bar.
The pressure can never reach a value greater than the supply pressure to the machine.
19. The field displaying the actual pressure applied to the scoring rolls.
20. The field displaying the set pressure applied to the scoring rolls. In this field, it is possible to enter the pressure value. By pressing the Enter button on the keyboard, the pressure will be updated
21. these buttons change the position of the slotting knives. Press and hold to move:
the slotting knives move apart slowly.
the slotting knives move closer slowly.
The position of the slotting knives is measured as the distance from the point of the left knife to the point of the right knife. The knives move evenly toward or away from the center of the machine. Spacing of the blades can range from 2 1/2” to 78 1/2“.
When one of the buttons displays a yellow arrow, it indicates that the slotting knives have travelled as far as possible.
22. Actual - the field displays the current distance between the slotting knives.
23. Set field - enter the distance at which the slotting knives should be spaced.
24. Set button - starts the slotting knives' movement to a position as entered in the Set field (19).
25. Calibration button – opens a window to enter the actual measurement between the knives. This will update the ‘Actual’ field.
Opening of the calibration window is only possible after entering Password 7415
26. STOP – the button stops slotting knives movement
27. Board Pass Motion Press and hold to move the corrugated sheet in or out of the machine. Press
for forward and
for reverse.
28. Board Guide Press and hold these buttons to change the position of the left, automatic, board guide.
The position of the left guide is measured as the distance from the inner wall of the guide to the center of the machine. It is possible to set the guide within the range 1 3/4” to 47”.
When one of the buttons displays a yellow arrow, it indicates that the left guide is in the extreme position.
29. Actual Position - the field displays the current position of the board guide.
30. Set - the field in which it is possible to enter the position at which the left board guide is to be set.
31. Set - this button moves the left guide to the position in the ‘Set’ field. (26).
32. Calibration button – opens a window to enter the actual distance from the center of the machine to the left guide. This will update the ‘Actual’ field (25).
Opening of the calibration window is only possible at the operator level or higher.
33. STOP – the button stops the left guide movement
34. Feeding Wheels: - these buttons are used to start or stop the feed rollers.
35. this button returns to the previous screen (Fig. 24).
36. this button leads to the next screen (Fig.26).
Fig. 28. Manual Movements Screen (2/3)
37. REFERENCING - this button moves the tool holder to his initial position.
When REFERENCING procedure is active backlight of the push button is on.
38. SCANNING - this button moves the scanner (tool holder) over the tools to define their actual positions and to check their quantities.
When SCANNING procedure is active backlight of the push button is on.
39. SETUP TOOLS - this button moves the longitudinal cutting knives and scoring wheels to their pre-set positions as entered in the setup fields.
When SETUP procedure is active backlight of the push button is on.
41. TOOLS CHANGE – service mode for tools change
42. Actual position - the fields display the actual position of each longitudinal knife/score.
The position of each lengthwise cutting knife/scoring wheel is measured as the distance from the blade to the center of the machine. It is possible to set the knives within the range of 0" to 47". It is possible to set the scoring rolls within the range of 1" to 47".
43. Target Position - Fields displaying the pre-determined position of each lengthwise knife. In these fields, it is possible to enter the position at which each knife is to be set from the center.
The knives should be spaced in the same order as presented in the graphics, otherwise the message "NOT POSSIBLE TO SET UP ALONG KNIVES [KNIFE NUMBER ]” will be displayed.
44. Up/down - pressing on this button will lift or lower the corresponding longitudinal tool.
-
- – tools gripper . Pressing on it will show pop-up GRIPPER
- – longitudinal knife. Pressing on it will show pop-up KNIFE
- – longitudinal score. Pressing on it will show pop-up SCORE
46. Pop-up GRIPPER
Fig. 30. Pop-up GRIPPER
47.
moves the gripper to the left;
moves the gripper to the right.
48. these buttons lock or release the score rollers gripper pin:
unlocks the gripper pin;
locks the gripper pin.
49. these buttons lock or release the longitudinal knives gripper pin:
unlocks the gripper pin;
locks the gripper pin.
50. Score sensor – sensor on the side of the scoring rolls. Detects holder with scoring roll.
51. Knife sensor – sensor on the side of the knives. Detects holder with knife.
52. Pop-up KNIFE
Fig.31. Pop-up KNIFE
53. Tool type - the currently installed knife type should be selected on the chosen holder.

54. Tool orientation - the current orientation of the installed tool.
The selected tool orientation is highlighted in green.
The operator, after manually changing the orientation of the longitudinal knife on the machine, must also mark/make this change in this window.
55. Brake - releases the brake of the selected tool holder.

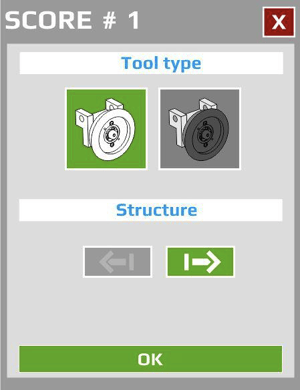
Fig.32. Pop-up SCORE
57. Tool type - the currently installed scoring wheel type should be selected on the chosen holder.
The operator must always confirm tool type change in this window. The selected tool type is highlighted in green.
58. Tool orientation - the current orientation of the installed tool.
Fig. 33. An example of tool orientation on the basis of creasing rollers: A - to the left of the fixing as viewed from the front of the machine, B - to the right of the fixing as viewed from the front of the machine
The selected tool orientation is highlighted in green.
The operator, after manually changing the orientation of the longitudinal score on the machine, must also mark/make this change in this window.
59. Brake - releases the brake of the selected tool holder.

Fig.34. Manual Movements screen (3/3)
60. ACROSS TOOL the buttons for the manual operation of the across cutting knife:
moves the knife to the left;
moves the knife to the right.
61. The graphic shows the transverse cutting knife. Pressing on the picture will lift or lower the knife. The lowering of the knife is indicated by a green "tick" .
62. REFERENCING - this button moves the across cutting knife to the home position.
When REFERENCING procedure is active backlight of the push button is on.
63. Output Wheels - The graphic shows the non-crush roller. Pressing on the picture lifts or lowers all the exit rollers.
64.Printer module 1 (option):
lift up/down the printer module 1.
or
indicates the position of printer module 1.
65. Printer module 2 (option):
lift up/down the printer module 2.
or
indicates the position of printer module 2.
66. GLUE HEADS - the graphics shows two the gluing heads. Pressing on a selected graphic will open this glue head valve.
Fig.35. The setting of gluing line (option)
67. Gluing line 1 – Set – Opening time of the gluing head for the gluing line 1 (Fig.35) (option).
68. Gluing line 1 – MAX – Cycle time of the gluing head for the gluing line 1 (Fig.35) (option).
69. Gluing line 2 – Set - Opening time of the gluing head for the gluing line 2 (Fig.35) (option).
70. Gluing line 2 – MAX – Cycle time of the gluing head for the gluing line 2 (Fig.35) (option).
Fig. 36. The Machine Parameters’ screen
71. Correction of the 1st pass – this parameter will affect the length of the first panel of a box. If any maintenance has taken place, this parameter may need to be changed.
72. Starting position of the beam above the board – distance between board surface and slotting knife as a start point for beam move
73. Slotting knives length – length of slotting knives mounted on the machine
74. Orientation of the board – rapid or smooth board passing in cycle
75.Circumference of measuring wheel 1 and 2 - the exact circumference of the measuring wheels.
76. Board move – Press and hold to move the corrugated sheet in or out of the machine. Press
for forward and
for reverse.
77. Set – the distance the board will travel after pressing the Encoder 1 or Encoder 2 buttons, measured by corresponding measuring wheel 1 or 2
78. V – speed parameters – this button open the pop-up Speed.
79. Pop-up Speed
Fig.37. Pop-up Speed
80. Feed rate – speed of the board movement in the cycle.
81. Across knife – speed of the across cutting knife in the cycle.
82. Scoring beam – speed of the slotting/scoring beam in the cycle.
83. Across tool – the buttons for the manual operation of the across cutting knife:
moves the knife to the left;
moves the knife to the right.
84. The graphic shows the transverse cutting knife. Pressing on the picture will lift or lower the knife. The lowering of the knife is indicated by a green "tick" .
85. Speed of across movement for the gluing – speed of the transversal tool movement for putting the glue in the cycle
86. External queue – enables the working with “Job Queue”
87. Encoder 1 / 2 – activates close loop control to set parameters for measuring wheel 1/2
Fig. 38. Counters and Alarms history
88. Total number of slot cuts – the number of cuts made by the slotting beam since machine inception.89. Service number of slotting knives cuts – the number of cuts made by the slotting beam since the last service.
90. Total number of cycles – the number of automatic work cycles since machine inception.
91. Total number of km – the number of kilometers of the corrugated measured by the encoders since machine inception.
92. Active alarms – displays active alarms / messages
93. Alarm history – the record of alarms / messages
‘FEFCO’ STYLE SCREENS - DESCRIPTION ON THE BASIS OF STANDARD STYLE 201
Following are the features available in the configuration screens for the FEFCO 0201 standard style.
Fig. 39. Main FEFCO 201 STANDARD style set-up screen
94. 0201 - the FEFCO style selected.
95. - saves the current box into the machine's memory with the name written in the RECIPE NAME field. Operation confirmed with message “Recipe added.”
96. Load to Freestyle – copies the current machine setting to the Freestyle
97. Add to Queue – adds the currently set box to the Job Queue. Operation confirmed with message “Order was added.”
98. Box dimensions – internal dimensions of the required box
99. Thickness – cardboard flute type
100. Score depth settings – Across – beam scoring depth in %:
The setting of the depth of the across score should be in range 0% to 100%:
- value 0% - without scoring between the slots;
- value 100% - max scoring depth between the slots;
101. Score depth settings – Along – + and - buttons for adjusting the depth of along scores on the board:
The setting for depth of the scores should be selected according to preference
102. Input board dimensions – Length and Width of the input sheet
103. Calculated board dimensions – Length and Width of the required board
104. Target Qty - the number of boxes to be made.
105. Actual Qty – the number of cartons already made. Next to it, there is a RESET button used to reset the count. To modify quantity done counter, use PLUS/MINUS buttons.
After completing the required number of cardboard boxes, the machine will stop. To continue production, the RESET button should be pressed, otherwise it will not be possible to start a new cycle.
106. Multiproduction – Max – shows the number of current boxes that can be produced from the length of the current sheet.
107. Multiproduction – Target – enter the number of boxes required from the sheet. The value may be lower or equal to the MAX value.
108. Printing – this button opens a pop-up to set parameters of printing (option).
109. Gluing – this button opens a pop-up to a set parameters of gluing (option).
110. Pop-up Gluing
Fig.40. Pop-up Gluing
111. Glue flap – glue flap length
112. Glue line from the edge – glue line position from the front edge of the bard
113. Gluing heads – select one or two heads to operate during the cycle
114. Offset for glue – offset between longitudinal scorings and glue line
115. Cutting off – this button opens a pop-up to a set cutting-off side
116. From the left and right side – cutting off the scrap from both sides
117. From the right side – cutting off the scrap from the right side of the input board
118. V – speed parameters – this button open the pop-up Speed described in 7.2.79
119. Scanning – this button opens a pop-up and starts the procedure of downloading data from an external scanner
120. Machine setup – this indicates that not all information has been entered or machine is not setup.
121. Machine adjusting – setting up the machine to set parameters
122. Machine ready to work – machine is setup to set parameters
123. Start – starts the automatic box production in the current style
124. Stop – stops the machine AFTER the whole board has passed through
Fig. 41. FEFCO 201 STANDARD style setup screen - advanced settings
125. Blue field - current value of the box panel dimension without allowances
126. White field - allowance value
127. Grey field - total value of panel dimension
SAVE ALLOWANCES button - pressing the button saves the allowances into the allowances database. The changes made to the allowances will be restored to their previous values after exiting the style. In order to save the allowances permanently, press the SAVE ALLOWANCES button for about 1 second, the saved allowances will be confirmed by the message “Allowances added.”
The button is active after logging into the operator's account
ALARMS, ERROR MESSAGES and FAILURES.
If the machine does not operate when required, it is likely that something has been overlooked. In this case, error messages will be displayed on the HMI panel.
EMERGENCY STOP – the machine was stopped by activation of the EMERGENCY STOP button or one of the limit switches at the protective covers, to eliminate the reason for this alarm, check if all the machine covers and casings are properly closed or turn the mushroom emergency stop switch clockwise (it will get unlocked). Then press the green RESET button.
LOW AIR PRESSURE - no or too low air pressure in the pneumatic system. It should be made sure that the machine is connected to the compressed air system at a suitable pressure level, and then an appropriate pressure in the machine should be set by turning the reduction valve of the compressed air preparation system.
TOO LOW AIR PRESSURE FOR CREASING ROLLS- too low or too high air pressure for longitudinal creases. The alarm is deleted with the RESET button.
ERROR SERVO DRIVE - BOARD – signals the occurrence of an alarm on the servo drive of the travel motor. The alarm is deleted with the RESET button.
ERROR SERVO DRIVE - LEFT CREASING BEAM - signals the occurrence of an alarm on the left servo drive of the creasing beam motor. The alarm is deleted with the RESET button.
ERROR SERVO DRIVE - RIGHT CREASING BEAM - signals the occurrence of an alarm on the right servo motor of the creasing beam. The alarm is deleted with the RESET button.
ERROR SERVO DRIVE - CREASING ROLLS AND KNIVES – signals the occurrence of an alarm on the servo drive of knives and creases. The alarm is deleted with the RESET button.
ERROR SERVO DRIVE - ACROSS KNIFE - signals a problem with the servo drive of the transverse knife motor. The alarm is deleted with the RESET button.
CREASING ROLLS SPACING FAULT – signals a problem with the precise positioning of the creasing rollers at the positions set. The alarm is deleted with the RESET button on the HMI touch panel.
KNIVES SPACING FAULT - signals a problem with the precise positioning of the longitudinal knives at the positions set. The alarm is deleted with the RESET button on the HMI touch panel.
ERROR DURING REFERENCING OR SPACING THE ALONG TOOL GRIPPER – signals a problem with homing or positioning of the longitudinal tool carriage. The alarm is deleted with the RESET button.
ERROR DURING REFERENCING OR POSITIONING THE ACROSS – indicates a problem with homing or positioning of the transverse tool. The alarm is deleted with the RESET button.
ERROR DURING REFERENCING OR POSITIONING THE CREASING BEAM - signals a problem with homing or positioning of the creasing beam. The alarm is deleted with the RESET button.
LEFT GUIDE SETUP FAULT – signals a problem with the precise positioning of the limiter in the set position. The alarm is deleted with the RESET button.
SLOTTING KNIVES SETUP FAULT - signals a problem with the precise positioning of the slotting knives in the set position. The alarm is deleted with the RESET button.
SLOTTING KNIVES ERROR - END POSITION REACHED – signals that the machine has reached the minimum position for the slotting knives during its setting. The alarm is deleted with the RESET button.
SLOTTING KNIVES ERROR - CREASING BEAM NOT REFERENCED – setting of the slotting knives is possible after the creasing beam has been homed. The alarm is deleted with the RESET button
MACHINE SETTING FAULT – signals a wrong setting of the machine for the production cycle. The alarm is deleted with the RESET button
NOT ENOUGH OF CREASING ROLLS – signals that the number of longitudinal creasing type is insufficient for a given box.
NOT ENOUGH OF ALONG CUTTING KNIVES - signals that the number of longitudinal knives is insufficient for making a given box.
NOT POSSIBLE TO SET UP CREASING ROLL [1…8] – the dimensions of the box introduced prevent the spacing of creases in a given position due to the required minimum distance between the tools. If this message occurs, change the orientation of the tools or increase dimensions of the box. The minimum distance between the tools is included in the attachment. The alarm is deleted with the RESET button.
SET POSITION OUTSIDE WORKING AREA - CREASING ROLL [1…8] – signals the setting of the longitudinal crease in an inaccessible zone. The alarm is deleted with the RESET button
NOT POSSIBLE TO SET UP ALONG KNIFE [1…8] – dimensions of the box entered prevent the spacing of knives in a given position due to the required minimum distance between the tools. If this message occurs, change the orientation of the tools or increase dimensions of the box. The minimum distance between the tools is shown in the attachment. The alarm is deleted with then RESET button.
SET POSITION OUTSIDE WORKING AREA - ALONG KNIFE [1…8] – signals the setting of the longitudinal knife in an inaccessible zone. The alarm is deleted with the RESET button.
CAN'T SETUP CREASING ROLLS – signals an attempt to set the longitudinal crease in an inaccessible area. The alarm is deleted with the RESET button.
CAN'T SETUP ALONG CUTTING KNIVES – signals an attempt to set the longitudinal knife in an inaccessible area. The alarm is deleted with the RESET button.
WRONG DATA FOR THE ACTIONS OF CREASING ROLLS – signals when the longitudinal action is too short for the longitudinal crease. The alarm is deleted with the RESET button.
WRONG DATA FOR THE ACTIONS OF ALONG KNIVES – signals a too short longitudinal action for the longitudinal knife. The alarm is deleted with the RESET button.
WRONG DATA FOR THE ACTIONS OF ACROSS TOOL - signals a too short transverse action for the transverse tool. The alarm is deleted with the RESET button.
NO SIGNAL THAT ACROSS KNIFE IS IN DOWN POSITION or NO SIGNAL THAT ACROSS KNIFE IS IN UP POSITION – signals an incorrect position of the transverse knife. In order to eliminate the cause, check air supply to the actuator, operation of the inductive sensor located on the actuator and mechanical operation of the actuator without air supply to the actuator. The alarm is deleted with the RESET button.
CREASING ROLLS AND KNIVES SEARCH FAULT – an alarm occurs during the search procedure for creases and knives. Check the drive system responsible for the spacing of creases and knives. The alarm is deleted with the RESET button.
WRONG NUMBER OF BOARDS TO MAKE – signals an input format that is too short in relation to the calculated format.
INPUT BOARD TOO SHORT – signals an input format that is too short in relation to the calculated format. The alarm is deleted with the RESET button.
INPUT BOARD TOO NARROW - signals an input format that is too narrow in relation to the calculated format. The alarm is deleted with the RESET button.
INPUT BOARD TOO LONG – signals that the length of the input format is more than 9000 mm. The alarm is deleted with of the RESET button.
INPUT BOARD TOO WIDE – signals that the width of the input format is more than 2400 mm. The alarm is deleted with the RESET button.
THERE IS PROBLEM WITH CARDBOARD MOVEMENT – signals the occurrence of an alarm when the format slips in the machine. The alarm is deleted with the RESET button.
BOARD INSIDE OF THE MACHINE – the message appears after pressing the START button or the HOME button (the guillotine homing button in the SETTINGS window) when there is a cardboard box or other object under the input or output laser sensor activating it. The alarm is deleted with the RESET button.
EMERGENCY STOP IS PRESSED - CONTROL PANEL HMI or EMERGENCY STOP IS PRESSED - REAR or EMERGENCY STOP IS PRESSED - RIGHT SIDE – the messages indicate that one of the safety switches on the machine has been pressed. The alarm is deleted with the RESET button.
SAFETY GUARD IS OPENED - LEFT FRONT or RIGHT FRONT or LEFT REAR or RIGHT REAR or LEFT REAR AT THE BOTTOM OR LEFT REAR AT THE BOTTOM – a message indicates the opening of covers on the machine. To reset the alarm, close the covers and press the RESET button.
WINDOW IS OPENED - LEFT or WINDOW IS OPENED - RIGHT –the opening of a window located on the side wall of the machine. To reset the alarm, close the open window and press the RESET button
REAR LEFT SAFETY GUARD NOT BLOCKED or REAR RIGHT SAFETY GUARD NOT BLOCKED – signals that the lock is not closed. To reset the alarm, press the RESET button.
8.0 Maintenance
General Notes
The machine operators can easily conduct most basic maintenance duties and preventative inspections as the machine is designed and built to operate with minimum maintenance to reduce stoppage periods.
However, some of the above mentioned operations are strongly recommended to be performed by the Manufacturer's qualified and experienced service technicians (it applies mainly to machine failures).
Complex maintenance and repair activities should not be performed without obtaining prior permission from the owner or manufacturer.
It is recommended to provide a Machine Repair Log where dates and types of repairs as well as preventative maintenance activities will be recorded.
Under no circumstances should anyone reach into the machine without taking all precautions to eliminate risk by shutting of all electrical and air supplies.
Particularly during maintenance operations or any other manual operations that may be required during preventive inspections, do not place any body parts in real and foreseeable danger zones before eliminating potential and foreseeable emergency situations.
ATTENTION: Work performed in the zones of feeding, cutting or scoring systems should be conducted only by qualified personnel and only after taking all precautionary measures. In the above mentioned zones the highest level of potential body injuries is possible.
All machine's operators performing maintenance or preventive activities must always wear protective clothing and ant-slip boots to limit the risk of slipping/falling.
Before performing any work at the machine, always check that cuffs are properly buttoned, zipped around the wrists or neatly tucked up. Personnel should always remember to protect their hair against being pulled into the machine by rollers and belts.
All maintenance or repair activities should be conducted only by qualified personnel who are trained to interpret machine failures, can read diagrams of installed systems and engineering drawings in such a way that all possible disassembly or assembly procedures connected with standard maintenance operations are performed professionally and, most of all, safely.
ATTENTION: Switchbox inspection and electrical systems maintenance can be performed only by certified electricians with valid training.
ATTENTION: Under no circumstances should any of the maintenance, repair or preventative activities be conducted when the machine is operating or is connected to a power supply unit.
Preventative Program, Periodical Inspection
AT THE BEGINNING OF EACH WORKING SHIFT CHECK IF:
- working space is clean, clear and safe;
- check the amount of solid impurities, leaks, and dust settling in/on the machine and all its components, if necessary clean it with a vacuum cleaner or a compressed air gun;
- clean the bottom knives in the counter-top;
- visually check the closing of all protective covers;
- sufficient level of lightning is provided to the working space;
- check the effectiveness of safety switches (EMERGENCY STOP), limit switches protecting movable covers and safety locks;
- Check AFTER 100 WORKING HOURS of the machine – or weekly:
- correct attachment and tightening of the load-bearing screws; check the tension of transport drive belt;
- clean the filter in the air preparation assembly
- Check AFTER 1,000 WORKING HOURS of the machine – or every 3 months:
- check effectiveness of the electric shock protection
- visually check the condition of mechanical components
- tighten all screw connections
- check the condition of the basic contact elements (contactors, relays), replace elements with worn connection surfaces.
9.0 Occupational and Safety Rules
The built-in safety features within the machine are designed to minimize any failures and to ensure that the safety requirements are met to minimize the risk of injury by maintaining a high level of safety.
The machine has many integrated safety features for the protection of operators and other personnel including:
- time-delay fire protection;
- limit switches to detect open/insecure covers and guards;
- safety lock with a latch
- decay phase sensor;
- covers and guards to protect from movable parts of the machine;
- easily accessible EMERGENCY STOP button installed on the main control panel;
- additional protection systems implemented in machine's control algorithm in order to halt the machine in potentially dangerous situations;
- the machine construction designed to provide the maximum level of safety for its operators.
Basic Safety Rules
Issues connected with safety rules and the evaluation of potential risk deriving from human-machine contact have been thoroughly covered in previous chapters of this service manual in which similar situations were presented. However, the importance of personnel safety is so profound that the Manufacturer has repeated the information once more here.
- All BOXMAT PRO operators must be acquainted with general safety rules implemented in the industrial workplace.
- In order to perform the optimal and safe machine use, this service manual should be read thoroughly and the user is strictly advised to follow all the instructions with a special focus on safety and warning signs.
- The final legal and financial responsibilities for all and any potential events derived from either the ignorance of the text of this service manual or the safety and occupational rules lies upon the purchaser. It is COMPLETELY AND ABSOLUTELY OBLIGATORY to read and follow these instructions.
- On the basis of the text included in this service manual and the knowledge derived from the manufacturer’s own product technology experience, the purchaser is strictly obliged to work out their own WORK STATION INSTRUCTIONS for their own machine operators.
- Each operator should read the text of this service manual before performing any work at the machine and should read any WORK STATION INSTRUCTION.
- Under no circumstances should the machine be operated by untrained personnel. The machine operators must be familiar with the occupational health and safety rules, and with a special focus on the risk created by the machine.
- Periodical preventative inspection of the fire protection system must be performed in the operated machine. The purchaser is fully responsible for making arrangements for conducting such inspection
- According to the manufacturer’s recommendations, the machine should be installed in the industrial environment only.
- Life threatening level of high power network voltage of 3 x 480 VAC, 50/60 Hz is delivered to the machine. As a result, all service or preventative activities should be performed only by well-trained personnel with qualifications required by law.
- UNDER NO CIRCUMSTANCES should any measures leading to decrease the machine safety status (such as blocking master switches or removing shields etc.) be undertaken by the purchaser or operator
- Any maintenance or other activities performed when the machine is running or when at a lowered standard of machine protection (while the shields are open or when the safety switches are defeated) must be kept to an absolute minimum before the full status of safety is restored.
- UNDER NO CIRCUMSTANCES should the machine be assembled, disassembled or transported by unqualified personnel or those unfamiliar with the safety rules included in this service manual as the said activities may lead to an accident or may become the cause of financial losses.
- The machine’s initial start-up should be conducted in the presence and under the supervision of Contractor’s agents.
- The machine’s test procedure, implemented always before the Buyer is entering the phase of full use of the machine, shall be performed only by an authorized person.
- Any change of any part, or use, of the machine which is inconsistent with that described in this service manual may lead to machine failures or become the cause of an accident.
- The machine's work parameters were pre-set by the Manufacturer in the most optimal way due to the installed rollers, cutting or scoring tools and electronic control systems. Any change in the machine's working parameters without the Manufacture's knowledge and permission may lead to an accident or poor performance.
Safety Conditions for the Personnel Directly Operating the Machine
ATTENTION: To prevent serious injury, it is essential that all covers and guards are kept in place to protect personnel from the dangers present from moving shafts, blades, knives, etc. while operating this box-making machine.
- It is advised that all and any personnel working with this or any other machinery should be trained and equipped to offer first aid assistance to any persons in the event of falls or accidents.
- The area surrounding this or any machine should not be blocked by any obstacles or waste product during its regular work cycle as this may cause stumbles, slips, falls or other accidents.
- The EMERGENCY STOP button is designed to be pressed at any time especially when an emergency shut-down is promptly needed.
- UNDER NO CIRCUMSTANCES should any moving parts of the machine be touched when working.
- UNDER NO CIRCUMSTANCES should any water based fire extinguisher equipment be used on or near the machine. Use only licensed non-water based firefighting agents and fire hazard protection products.
- UNDER NO CIRCUMSTANCES should any guards or covers be removed during machine work cycle.
- UNDER NO CIRCUMSTANCES should the operators stand or climb on the guards or covers.
- UNDER NO CIRCUMSTANCES should the operators stand or climb on the guards or covers.
- UNDER NO CIRCUMSTANCES should any oil, solvent or other caustic or toxic substances be allowed to come into contact with the machine.
- UNDER NO CIRCUMSTANCES should mobile phones be used near the machine direct environment.
- UNDER NO CIRCUMSTANCES should naked flames be used in the machine direct environment.
- UNDER NO CIRCUMSTANCES should cigarettes be smoked in the machine direct environment.
- UNDER NO CIRCUMSTANCES should alcohol be consumed in the machine direct environment nor should personnel under the influence of alcohol operate the machine.
- UNDER NO CIRCUMSTANCES should personnel consume meals in the machine direct environment.
- IT IS ESSENTIAL to use ALL covers and guards designed for the machine.
- IT IS ESSENTIAL that any accidents or machine failures should be promptly reported to the management.
- IT IS ESSENTIAL to use suitable working clothing to limit the possibility of being snagged or dragged into the machine.
- IT IS ESSENTIAL to wear protective gloves while operating the machine.
- IT IS ESSENTIAL to wear anti-slip, safety footwear.
- IT IS ESSENTIAL to use hair covering to minimise the possibility of being snagged or pulled into the machine.
- IT IS ESSENTIAL to keep the floor around the machine clean and clear of all debris and waste material.
- IT IS ESSENTIAL to use hearing protection.
- IT IS RECOMMENDED to use the EMERGENCY STOP button whenever there is a situation where the machine or the operator are at risk.
- Careless handling of the machine during transport and/or relocation may lead to severe injuries or accidents.
- Only suitably trained personnel taking special precautionary measures can perform certain tasks inside the machine. In these areas there is increased risk of severe injuries.
- At no time should operators climb on the machine.
- The switchbox doors should always be closed even if the machine is not in operation.
- The machine operators are strongly advised to work only in the safe work zone which is outlined in the drawing below:
Fig. 42. Tolerable boundaries of work zone during work cycle performed by Boxmat PRO. The area in which the machine's operators are not allowed to stay and perform their tasks at the machine was marked with the use of red color -the clearance zone around the machine should be no less than 59”.
Workplace Safety Rules During Maintenance, Repair, and Preventative Activities
- UNDER NO CIRCUMSTANCES should any service, maintenance or preventative measures be undertaken without full disconnection from supply network
- UNDER NO CIRCUMSTANCES should the machine be lubricated, cleaned or maintained while it is in operation.
- Switchbox and electrical systems maintenance can be performed only by suitably trained and qualified electrical engineers.
- Under no circumstances should the machine maintenance be conducted by unqualified or inexperienced engineers who are unfamiliar with the machine electrical wiring.
- Personnel performing maintenance activities should wear suitable protective clothing.
- Under no circumstances should the electrical system be modified in any way.
- The doors of the control system cabinet should be always locked and only authorized personnel should have access to the key.
Summary
Suitable measures should be taken during machine operation, its transport and installation procedures, and the repair, maintenance and preventative routines, to prevent the following situations:
- The machine should not be used in any way other than described herein;
- The machine should not be connected electrically with disregard to the provisions included herein;
- The machine should not be used inappropriately or used by untrained personnel;
- The machine should not be used with unsuitable materials;
- There must be sufficient suitable maintenance;
- There must be no unauthorized changes or alterations by unqualified or untrained personnel;
- There must be no use of non-original spare parts;
- There must be no personnel activities breaching the law and/or the regulations applicable to the workplace, as well as the provisions included in this service manual.
10.0 Electrical Documentation
10.1 POWER SUPPLY PARAMETERS – TECHNICAL DATASupply voltage 3 x 230 VAC; 50/60 Hz
Control voltage 24 VDC
Maximum power consumption 5.5 kW
10.2 LIST OF ELECTRICAL APPARATUSSee enclosure.
10.3 WIRING DIAGRAMSee enclosure.
11.0 Pneumatic Documentation
11.1. TECHNICAL DATA
Working pressure 0.6 – 0.8 MPa
Filtration accuracy 20 μм
Required class of working medium activity
4-4-4 according to ISO8573-1 standards
11.2 PRINCIPLE OF OPERATION
The working medium which is introduced to the system with the help of pressure reducing valve is subject to the initial filtration and then the reduction procedure due to which it is reduced to the required level. Then with the help of distribution valve controlled by the electro-pneumatic system the medium is delivered to the adequate servo-motor and as a result the said servo-motor is put in motion. Finally, the servo-motor motion will cause the relocation of razor blade due to which the glue flap will be cut off.
ATTENTION: The purchaser is strongly advised to maintain the adequate 4-4-4 class of air cleanliness according to ISO8573-1 requirements even though the Manufacturer equipped the machine in the compressed-air preparation system.
The above mentioned pneumatic system does not require an extreme amount of attention, though, the user is obliged to control the level of condensation water in compressed-air filter tank periodically. If the presence of water is found, it should be emptied. If the significant amount of solid impurities in the tank are found, the tank must be dismantled, and then cleaned out with suitable cleaners. After cleaning out it should be aired with compressed-air and refitted. The detailed description of compressed-air system can be found in part titled CONTROLS AND INDICATORS AVAILABLE for OPERATOR.
11.4. PNEUMATIC SYSTEM DIAGRAM
See enclosure.
12.0 Utilization and Machine-Breaking
12.1 GENERAL NOTESIntroduced changes in law provisions or in process standards, which could not have been foreseen earlier, may become the cause of utilization and machine- breaking. This issue applies also to the machine's replaced or repaired parts and systems. In consequence, the purchaser is solely responsible for conducting the above mentioned procedures according to the binding provisions of law. It should be noted, however, that all machine's parts can be fully recycled.
12.2 WASTE MATERIAL
Hazardous waste should be always utilized by the companies which specialize in dealing with this kind of issue on a regular basis. The detailed list of type of waste produced by the machine in its life span is attached below:
- cardboard, corrugated board and other waste products;
- worn-out spare parts, which are divided into types of material from which they are made.
- All waste material deriving from machine parts' replacement or servicing even partially contaminated by grease cannot be discarded along with the industrial waste products.
ATTENTION: It is strictly forbidden to place hazardous waste directly into the waste containers or use the municipal waste collectors to dispose of it.
12.3 PHASES OF DISMANTLING PROCEDURE IMPLEMENTED for MACHINE-BREAKING
- Use MASTER SWITCH to switch off the machine;
- Machine must be placed in stable position on the floor.;
- Disconnect the machine from both pneumatic and electric power sources;
- Detach from the machine and disassemble both work tables (if they were ordered);
- Disconnect the flexible connections made of plastic and rubber, then utilize them with the help of companies which specialize in dealing with this kind of waste;
- Disconnect wiring systems and electrical equipment and then utilize them with the help of companies which specialize in dealing with this kind of waste.
- Divide metal waste into steel and non-ferrous and then break them up for scrap with the help of companies which specialize in dealing with this kind of waste.
13.0 Enclosures
Rating Plate
14.0 Additional Machine Documents